A comprehensive list of causes and solutions for submersible pump failures in water knowledge
发布时间:2024-05-24 09:52:00 点击:122
(1) Reasons and treatment methods for insufficient flow or no water output during the operation of submersible pumps:
(1) The installation height of the water pump is too high, resulting in insufficient immersion depth of the impeller and a decrease in the water output of the water pump; The allowable deviation for controlling the installation elevation of the water pump should not be arbitrarily expanded.
(2) The direction of rotation of the water pump is opposite. Before the trial operation of the water pump, the electric motor should be idling and the direction should be checked to make it consistent with the water pump; If the above situation occurs during use, check whether the phase sequence of the power supply has changed.
(3) The water outlet valve cannot be opened. Inspect valves and regularly maintain them.
(4) The water outlet pipeline is not smooth or the impeller is blocked. Clean up blockages in pipelines and impellers, and frequently salvage debris from the reservoir.
(5) The wear-resistant ring at the lower end of the water pump is severely worn or blocked by debris. Clean up debris or replace wear rings.
(6) The density or viscosity of the pumped liquid is too high. Identify the causes of water quality changes and implement measures to address them.
(7) The impeller is detached or damaged. Reinforce or replace the impeller.
(8) When multiple water pumps share the same pipeline output, one-way valves are not installed or the sealing of one-way valves is not tight. After checking the cause, install or replace the one-way valve.
(2) The operation of the submersible pump exhibits abnormal vibration and instability, mainly due to:
(1) The anchor bolts of the water pump base are not tightened or loose; Tighten all anchor bolts evenly;
(2) The water outlet pipeline is not supported independently, and the vibration of the pipeline affects the water pump; Provide independent and stable support for the outlet pipe of the water pump to prevent the flange of the outlet pipe from bearing weight.
(3) Impeller quality imbalance, even damage or loose installation; Repair or replace the impeller;
(4) The upper and lower bearings of the water pump are damaged; Replace the upper and lower bearings of the water pump.
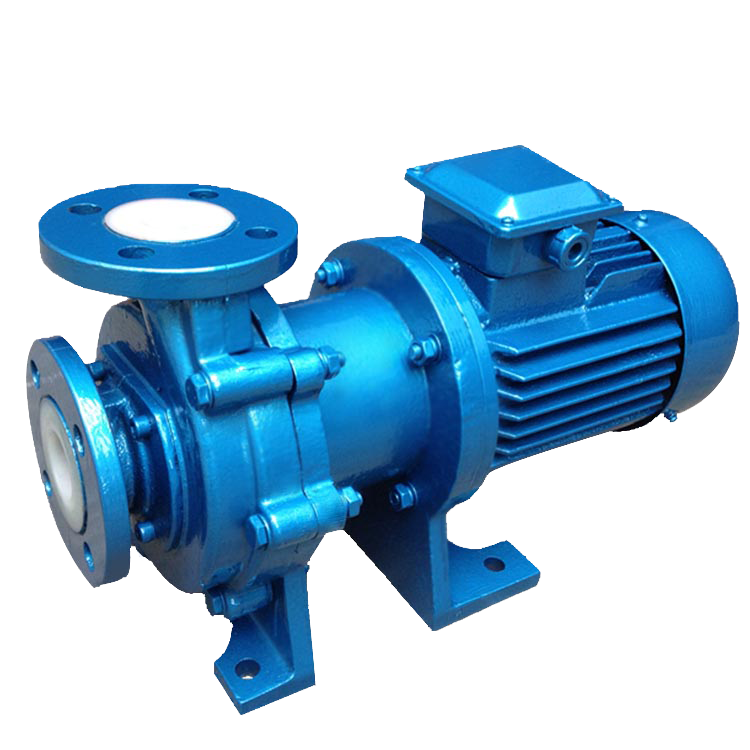
III. The main reasons for motor overload or overheating caused by excessive current in submersible pumps:
(1) Low or high working voltage; Check the power supply voltage and adjust the output voltage.
(2) There is friction between dynamic and static components inside the water pump or friction between the impeller and the sealing ring; Determine the position of friction components and eliminate faults.
(3) Low head and high flow rate result in motor power not matching the characteristics of the water pump; Adjust the valve to reduce the flow rate and match the motor power with the water pump.
(4) The pumping density is high or the viscosity is high; Check the causes of water quality changes and change the working conditions of the water pump
(5) Bearing damage; Replace the bearings at both ends of the motor
4. The main reasons and treatment methods for the low insulation resistance of submersible pumps:
(1) When installing the power cord, the end is submerged in water or the power cord or signal cord is damaged, causing water ingress; Replace the cable or signal line and dry the motor.
(2) Mechanical seals worn or not installed properly; Replace the upper and lower mechanical seals and dry the motor.
(3) O-ring aging and loss of function; Replace all sealing rings and dry the motor.
5. In the pipeline of the submersible pump, there is often obvious water leakage at the connection of the pipeline or flange. Reasons and treatment methods:
① The pipeline itself has defects and has not undergone pressure testing;
② The gasket joint at the flange connection is not properly handled;
③ The flange bolts were not tightened in a reasonable manner; Defective pipes should be repaired or even replaced. If the center deviation of the connecting pipes is too large, they should be removed and rearranged. After alignment, the connecting bolts should be inserted and tightened in a basically free state. After all pipelines are installed, the system's pressure resistance strength and leakage test should be conducted. It must be replaced with a new one.
Internal leakage of six submersible pumps:
When the submersible pump leaks, it causes insulation damage, bearing immersion, and alarm system alarm, forcing the unit to stop running.
The main reason is that the dynamic seal (mechanical seal) or static seal (cable inlet special seal, 0-type sealing ring) of the submersible pump is damaged, causing water seepage, and the power or signal cable is damaged, causing water seepage.
Various alarm signals such as water immersion, leakage, humidity, etc. alarm shutdown;
Before installation, the quality of each sealing component should be checked;
Ensure good contact between the end faces of each sealing component during installation;
Before operation, check the insulation resistance between phases and ground of the motor, as well as whether the sensing components of each alarm system are intact.
When the above faults occur during operation, replace all damaged seals and cables and dry the motor. Seals and cables that have been disassembled must not be reused.
When the submersible pump stops, it reverses:
1. After the power outage of the water pump motor, the water pump will reverse, mainly due to the failure of the check valve or flap valve in the outlet pipeline.
2. Before installation, the troubleshooting measures should be checked. The installation direction of the check valve should be correct, the center of the tapping valve should be aligned, and the opening and closing should be flexible and flexible. Regularly inspect the check valve or flap door during operation, repair or replace the damaged parts with quality assurance check valves or flaps.
(1) The installation height of the water pump is too high, resulting in insufficient immersion depth of the impeller and a decrease in the water output of the water pump; The allowable deviation for controlling the installation elevation of the water pump should not be arbitrarily expanded.
(2) The direction of rotation of the water pump is opposite. Before the trial operation of the water pump, the electric motor should be idling and the direction should be checked to make it consistent with the water pump; If the above situation occurs during use, check whether the phase sequence of the power supply has changed.
(3) The water outlet valve cannot be opened. Inspect valves and regularly maintain them.
(4) The water outlet pipeline is not smooth or the impeller is blocked. Clean up blockages in pipelines and impellers, and frequently salvage debris from the reservoir.
(5) The wear-resistant ring at the lower end of the water pump is severely worn or blocked by debris. Clean up debris or replace wear rings.
(6) The density or viscosity of the pumped liquid is too high. Identify the causes of water quality changes and implement measures to address them.
(7) The impeller is detached or damaged. Reinforce or replace the impeller.
(8) When multiple water pumps share the same pipeline output, one-way valves are not installed or the sealing of one-way valves is not tight. After checking the cause, install or replace the one-way valve.
(2) The operation of the submersible pump exhibits abnormal vibration and instability, mainly due to:
(1) The anchor bolts of the water pump base are not tightened or loose; Tighten all anchor bolts evenly;
(2) The water outlet pipeline is not supported independently, and the vibration of the pipeline affects the water pump; Provide independent and stable support for the outlet pipe of the water pump to prevent the flange of the outlet pipe from bearing weight.
(3) Impeller quality imbalance, even damage or loose installation; Repair or replace the impeller;
(4) The upper and lower bearings of the water pump are damaged; Replace the upper and lower bearings of the water pump.
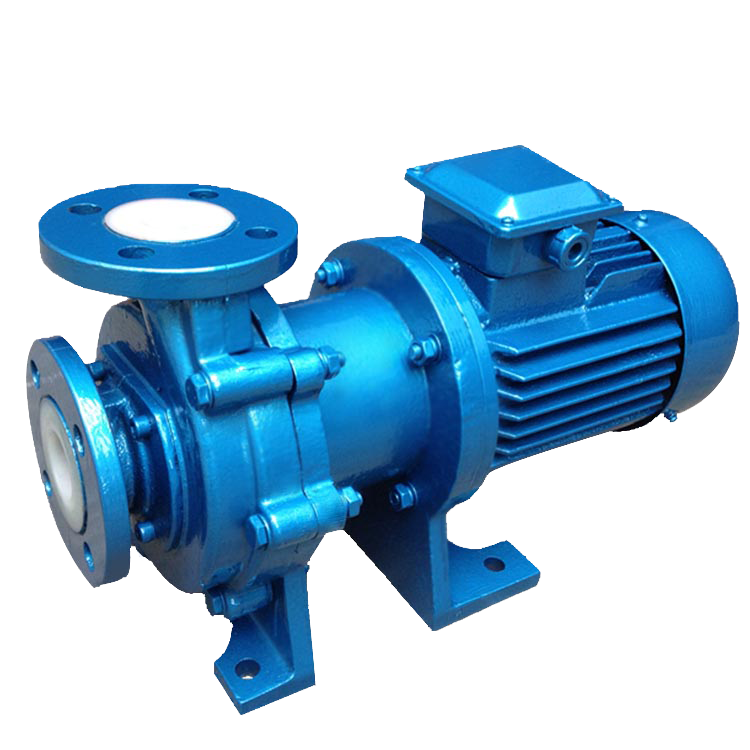
III. The main reasons for motor overload or overheating caused by excessive current in submersible pumps:
(1) Low or high working voltage; Check the power supply voltage and adjust the output voltage.
(2) There is friction between dynamic and static components inside the water pump or friction between the impeller and the sealing ring; Determine the position of friction components and eliminate faults.
(3) Low head and high flow rate result in motor power not matching the characteristics of the water pump; Adjust the valve to reduce the flow rate and match the motor power with the water pump.
(4) The pumping density is high or the viscosity is high; Check the causes of water quality changes and change the working conditions of the water pump
(5) Bearing damage; Replace the bearings at both ends of the motor
4. The main reasons and treatment methods for the low insulation resistance of submersible pumps:
(1) When installing the power cord, the end is submerged in water or the power cord or signal cord is damaged, causing water ingress; Replace the cable or signal line and dry the motor.
(2) Mechanical seals worn or not installed properly; Replace the upper and lower mechanical seals and dry the motor.
(3) O-ring aging and loss of function; Replace all sealing rings and dry the motor.
5. In the pipeline of the submersible pump, there is often obvious water leakage at the connection of the pipeline or flange. Reasons and treatment methods:
① The pipeline itself has defects and has not undergone pressure testing;
② The gasket joint at the flange connection is not properly handled;
③ The flange bolts were not tightened in a reasonable manner; Defective pipes should be repaired or even replaced. If the center deviation of the connecting pipes is too large, they should be removed and rearranged. After alignment, the connecting bolts should be inserted and tightened in a basically free state. After all pipelines are installed, the system's pressure resistance strength and leakage test should be conducted. It must be replaced with a new one.
Internal leakage of six submersible pumps:
When the submersible pump leaks, it causes insulation damage, bearing immersion, and alarm system alarm, forcing the unit to stop running.
The main reason is that the dynamic seal (mechanical seal) or static seal (cable inlet special seal, 0-type sealing ring) of the submersible pump is damaged, causing water seepage, and the power or signal cable is damaged, causing water seepage.
Various alarm signals such as water immersion, leakage, humidity, etc. alarm shutdown;
Before installation, the quality of each sealing component should be checked;
Ensure good contact between the end faces of each sealing component during installation;
Before operation, check the insulation resistance between phases and ground of the motor, as well as whether the sensing components of each alarm system are intact.
When the above faults occur during operation, replace all damaged seals and cables and dry the motor. Seals and cables that have been disassembled must not be reused.
When the submersible pump stops, it reverses:
1. After the power outage of the water pump motor, the water pump will reverse, mainly due to the failure of the check valve or flap valve in the outlet pipeline.
2. Before installation, the troubleshooting measures should be checked. The installation direction of the check valve should be correct, the center of the tapping valve should be aligned, and the opening and closing should be flexible and flexible. Regularly inspect the check valve or flap door during operation, repair or replace the damaged parts with quality assurance check valves or flaps.