164 Technical Questions and Answers for Water Pump (1-30)
发布时间:2024-05-31 08:54:00 点击:95
1. What is a pump? Answer: A pump is a mechanical device that converts the mechanical energy of the prime mover into the energy of pumping liquid.
2. What is power? Answer: The work done per unit time is called power.
3. What is effective power? In addition to the energy loss and consumption of the machinery itself, the actual power obtained by the liquid through the pump per unit time is called effective power.
4. What is shaft power? Answer: The power transmitted by the motor to the pump shaft is called shaft power.
5. Why is it said that the power transmitted from the motor to the pump is always greater than the effective power of the pump?
Answer:
1) During the operation of a centrifugal pump, a portion of the high-pressure liquid inside the pump needs to flow back to the pump inlet or even leak out of the pump, resulting in a loss of some energy;
2) When liquid flows through the impeller and pump casing, changes in flow direction and velocity, as well as collisions between fluids, also consume some energy;
3) The mechanical friction between the pump shaft, bearings, and shaft seals also consumes a portion of energy; Therefore, the power transmitted by the motor to the shaft is always greater than the effective power of the shaft.
6. What is the total efficiency of a pump? Answer: The ratio of the effective power of the pump to the shaft power is the total efficiency of the pump.
7. What is the flow rate of a pump? What symbol is used to represent it?
Flow rate refers to the amount of liquid (volume or mass) flowing through a certain section of a pipeline per unit of time. The flow rate of the pump is represented by "Q".
8. What is the head of a pump? What symbol is used to represent it? Answer: Head refers to the energy gain per unit weight of fluid. The head of the pump is represented by "H".
9. What are the characteristics of chemical pumps?
Answer:
1) Capable of adapting to the requirements of chemical processes;
2) Corrosion resistance;
3) High temperature and low temperature resistance;
4) Wear resistance and erosion resistance;
5) Reliable operation;
6) No leakage or minimal leakage;
7) Can transport liquids in critical states;
8) Has anti cavitation performance;
10. How many types of commonly used mechanical pumps are classified according to their working principles?
Answer:
1) Vane pump: When the pump shaft rotates, it drives various impeller blades to apply centrifugal or axial force to the liquid, conveying it to pipelines or containers, such as centrifugal pumps, vortex pumps, mixed flow pumps, and axial flow pumps.
2) Positive displacement pump. A pump that utilizes the continuous variation of the volume product of the pump cylinder to transport liquids, such as reciprocating pumps, piston pumps, gear pumps, and screw pumps;
3) Other types of pumps. An electromagnetic pump that utilizes electromagnetic transmission of liquid electrical conductors; Pumps that use fluid energy to transport liquids, such as jet pumps, air elevators, etc.
11. What aspects of treatment should be carried out before the maintenance of chemical pumps?
Answer:
1) Before maintenance of machinery and equipment, it is necessary to stop, cool down, relieve pressure, and cut off the power supply;
2) Machines and equipment with flammable, explosive, toxic, and corrosive media must be cleaned, neutralized, replaced, analyzed and tested before construction can proceed;
3) When repairing equipment, machinery, or pipelines with flammable, explosive, toxic, or corrosive media, the material inlet and outlet valves must be cut off, and blind plates must be installed.
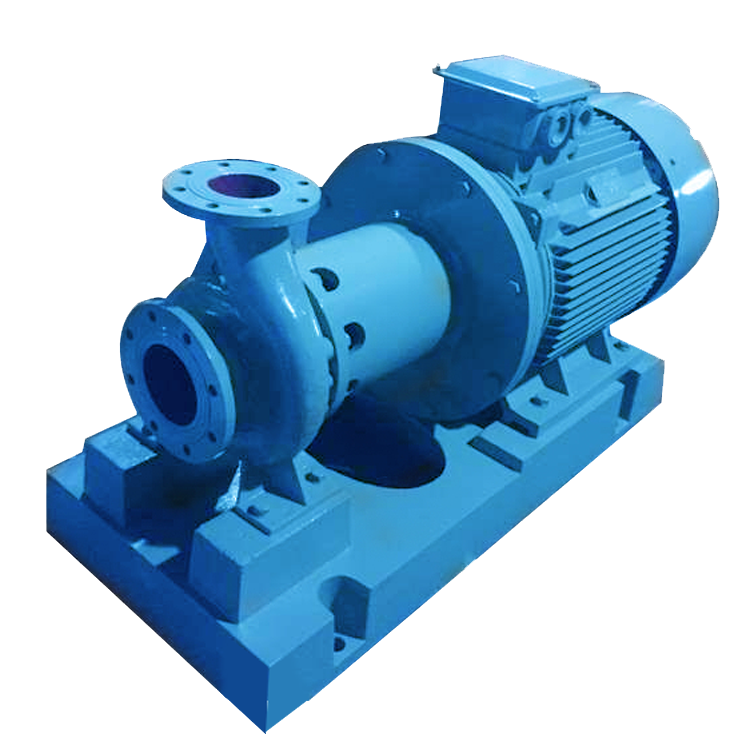
12. What process conditions should be met before the maintenance of chemical pumps? Answer: 1) Parking; 2) Cooling down; 3) Pressure relief; 4) Cut off the power supply; 5) Permutation;
13. What are the general principles for mechanical disassembly? Answer: In general, the parts should be disassembled first from the outside to the inside, from top to bottom, and in sequence. For overall parts, it is best to disassemble them as a whole.
14. What is the power loss inside a centrifugal pump?
Answer: There are three types of losses: hydraulic loss, volumetric loss, and mechanical loss.
1) Hydraulic loss: When the fluid flows in the pump body, if the flow channel is smooth, the resistance will be smaller, while if the flow channel is rough, the resistance will be greater. When the water enters the rotating impeller or flows out of the impeller, collisions and vortices will also occur, causing losses. The above two types of losses are called hydraulic losses.
2) Volume loss: The impeller is rotating, while the pump body is stationary. A small portion of the fluid flows back to the inlet of the impeller in the gap between the impeller and the pump body;
In addition, a portion of the fluid flows back from the balance hole to the impeller inlet, or leaks from the shaft seal.
If it is a multi-stage pump, there will also be some leakage from the balance plate, and these losses are called volume losses;
3) Mechanical loss: When the shaft rotates, it will rub against bearings, packing, etc. The impeller will rotate inside the pump body, and the front and rear cover plates of the impeller will rub against the fluid, consuming a portion of power. These losses caused by mechanical friction are collectively referred to as mechanical losses.
15. What is the basis for finding balance of rotors in production practice?
Answer: Depending on the number of revolutions and structure, static balance method or dynamic balance method can be used.
The balance of a rotating body can be solved using the static balance method. Static balance can only balance the imbalance of the center of gravity of a rotating body (i.e., eliminate torque), but cannot eliminate the imbalance couple.
Therefore, static equilibrium is generally only used for disc-shaped rotating bodies with relatively small diameters. For rotating bodies with larger diameters, dynamic balancing problems are often common and prominent, so balancing treatment is necessary.
Therefore, static equilibrium is generally only applicable to disc-shaped rotating bodies with relatively small diameters. For rotating bodies with larger diameters, dynamic balancing problems are often prominent and common, so balancing treatment is necessary.
16. What is balance? How many types of balance are there? Answer: The work of eliminating the imbalance of rotating parts or components is called balancing; 2) Balance can be divided into two types: static balance and dynamic balance.
17. What is static equilibrium? Answer: The method of finding balance is called static balance, which involves measuring the front position of the rotating part's imbalance on some specialized fixtures without the need for rotation, and also determining the position and magnitude of the balance force to be applied.
18. What is dynamic balance? Answer: When rotating parts, balancing not only the centrifugal force generated by the eccentricity, but also the balance of the force couple moment composed of the centrifugal force is called balance.
Dynamic balancing is generally used for machines with high speed, large diameter, and particularly strict working accuracy requirements, and precise dynamic balancing must be performed.
19. How to determine the weight orientation of the balanced part when performing static balancing of rotating parts?
Answer: First, let the balanced part freely roll on the balancing fixture several times. If the last rotation is clockwise, the center of gravity of the part must be on the right side of the vertical centerline (due to friction resistance). At this point, make a mark with a white chalk at the lowest point of the part, and then let the part roll freely. If the last roll is completed in a counterclockwise direction, the center of gravity of the balanced part must be on the left side of the vertical centerline. Similarly, make a mark with a white chalk, and the center of gravity recorded twice is the biased direction.
20. When performing static balancing of rotating parts, then determine the size of the balancing weight?
Answer: First, turn the biased position of the part to the horizontal position, and add an appropriate weight at the maximum circle of the symmetrical position on the opposite side.
When choosing to add appropriate weight, one should consider the location of this point and whether it is possible to balance and reduce weight in the future. After adding appropriate weight, keep it in a horizontal position or slightly swing it, and then reverse the part 180 degrees to maintain its horizontal position. Repeat this process several times until the appropriate weight is determined to remain unchanged. Then, remove the appropriate weight and weigh it, which determines the gravity of the balance weight.
21. What are the types of mechanical rotor imbalance? Answer: Static imbalance, dynamic imbalance, and mixed imbalance.
22. How to measure the bending of the pump shaft? Answer: After the shaft is bent, it will cause imbalance of the rotor and wear of the dynamic and static parts. Place small bearings on V-shaped iron and large bearings on roller brackets. The V-shaped iron or bracket should be placed firmly, and then support the dial gauge with the stem pointing towards the shaft center. Slowly rotate the pump shaft. If there is bending, the dial gauge has a maximum and minimum reading per revolution. The difference between the two readings indicates the maximum radial runout of the bending, also known as wobbling.
The bending degree of the shaft is half of the shaking degree, and the radial runout of the shaft generally does not exceed 0.05mm in the middle and 0.02mm at both ends.
23. What are the three main types of mechanical vibration causes?
Answer:
1) Structural aspect: caused by manufacturing design defects;
2) In terms of installation: mainly caused by improper assembly and maintenance assembly;
3) In terms of operation, due to improper operation, mechanical damage or excessive wear.
24. Why is it said that rotor misalignment is an important reason for abnormal vibration of the rotor and early damage to the bearings?
Answer: Due to installation errors, rotor manufacturing, deformation after bearing, environmental temperature changes, and other factors, rotor misalignment may occur. Poor rotor alignment in the shaft system can change the actual working position of the rotor journal and bearings due to changes in coupling force. This not only changes the working state of the bearings, but also reduces the natural frequency of the rotor shaft system. Therefore, rotor misalignment is an important reason for abnormal rotor vibration and early bearing damage.
25. What are the standards for measuring and rechecking the roundness and taper of the shaft neck?
Answer: The ovality and taper of the measured and rechecked sliding bearing shaft diameter should meet the technical requirements, and generally should not exceed one thousandth of the diameter. The ovality and taper of the shaft diameter of the rolling bearing shall not exceed 0.05mm.
26. What precautions should be taken when assembling chemical pumps?
Answer:
1) Whether the pump shaft is bent, deformed, etc;
2) Whether the rotor balance condition meets the standards;
3) The gap between the impeller and pump casing;
4) Whether the compression amount of the mechanical seal buffer compensation mechanism meets the requirements;
5) The concentricity of the pump rotor and volute;
6) Is the centerline of the pump impeller flow passage aligned with the centerline of the volute flow passage;
7) Adjustment of clearance between bearings and end caps;
8) Adjustment of the gap between the sealing parts;
9) Whether the assembly of the transmission system motor and the variable (increase/decrease) speed reducer meets the standards;
10) Align the coaxiality of the coupling;
11) Whether the gap between the retaining rings meets the standard;
12) Is the tightening force of each connecting bolt appropriate.
27. What is the purpose of pump maintenance? What are the requirements?
Answer: Objective: To eliminate problems that exist after long-term operation by inspecting and repairing mechanical pumps.
The requirements are as follows:
1) Eliminate and adjust large gaps caused by wear and corrosion inside the pump;
2) Eliminate dirt, dirt, and rust inside the pump;
3) Repair or replace parts that do not meet the requirements or have defects;
4) The rotor balance test is qualified;
5) Check the coaxiality between the pump and the drive machine and ensure it meets the standards;
6) The test run is qualified, the information is complete, and it meets the requirements of process production.
28. What is the reason for the excessive power consumption of the pump?
Answer:
1) The total head does not match the pump head;
2) The density and viscosity of the medium do not match the original design;
3) Inconsistent or bent pump shaft and prime mover axis;
4) There is friction between the rotating part and the fixed part;
5) Wear on the impeller retaining ring;
6) Improper installation of seals or mechanical seals;
29. What are the reasons for rotor imbalance?
Answer:
1) Manufacturing errors, uneven material density, different axial degrees, non rounded corners, and uneven heat treatment;
2) Incorrect assembly: The centerline and axis of the assembled components are different from the axis;
3) The rotor undergoes uneven deformation and wear, and the shaft deforms under operation and temperature.
30. What is a dynamically unbalanced rotor? Answer: There exists a rotor with equal size, opposite direction, and unbalanced particles combined into two force couples that are not on a straight line.
2. What is power? Answer: The work done per unit time is called power.
3. What is effective power? In addition to the energy loss and consumption of the machinery itself, the actual power obtained by the liquid through the pump per unit time is called effective power.
4. What is shaft power? Answer: The power transmitted by the motor to the pump shaft is called shaft power.
5. Why is it said that the power transmitted from the motor to the pump is always greater than the effective power of the pump?
Answer:
1) During the operation of a centrifugal pump, a portion of the high-pressure liquid inside the pump needs to flow back to the pump inlet or even leak out of the pump, resulting in a loss of some energy;
2) When liquid flows through the impeller and pump casing, changes in flow direction and velocity, as well as collisions between fluids, also consume some energy;
3) The mechanical friction between the pump shaft, bearings, and shaft seals also consumes a portion of energy; Therefore, the power transmitted by the motor to the shaft is always greater than the effective power of the shaft.
6. What is the total efficiency of a pump? Answer: The ratio of the effective power of the pump to the shaft power is the total efficiency of the pump.
7. What is the flow rate of a pump? What symbol is used to represent it?
Flow rate refers to the amount of liquid (volume or mass) flowing through a certain section of a pipeline per unit of time. The flow rate of the pump is represented by "Q".
8. What is the head of a pump? What symbol is used to represent it? Answer: Head refers to the energy gain per unit weight of fluid. The head of the pump is represented by "H".
9. What are the characteristics of chemical pumps?
Answer:
1) Capable of adapting to the requirements of chemical processes;
2) Corrosion resistance;
3) High temperature and low temperature resistance;
4) Wear resistance and erosion resistance;
5) Reliable operation;
6) No leakage or minimal leakage;
7) Can transport liquids in critical states;
8) Has anti cavitation performance;
10. How many types of commonly used mechanical pumps are classified according to their working principles?
Answer:
1) Vane pump: When the pump shaft rotates, it drives various impeller blades to apply centrifugal or axial force to the liquid, conveying it to pipelines or containers, such as centrifugal pumps, vortex pumps, mixed flow pumps, and axial flow pumps.
2) Positive displacement pump. A pump that utilizes the continuous variation of the volume product of the pump cylinder to transport liquids, such as reciprocating pumps, piston pumps, gear pumps, and screw pumps;
3) Other types of pumps. An electromagnetic pump that utilizes electromagnetic transmission of liquid electrical conductors; Pumps that use fluid energy to transport liquids, such as jet pumps, air elevators, etc.
11. What aspects of treatment should be carried out before the maintenance of chemical pumps?
Answer:
1) Before maintenance of machinery and equipment, it is necessary to stop, cool down, relieve pressure, and cut off the power supply;
2) Machines and equipment with flammable, explosive, toxic, and corrosive media must be cleaned, neutralized, replaced, analyzed and tested before construction can proceed;
3) When repairing equipment, machinery, or pipelines with flammable, explosive, toxic, or corrosive media, the material inlet and outlet valves must be cut off, and blind plates must be installed.
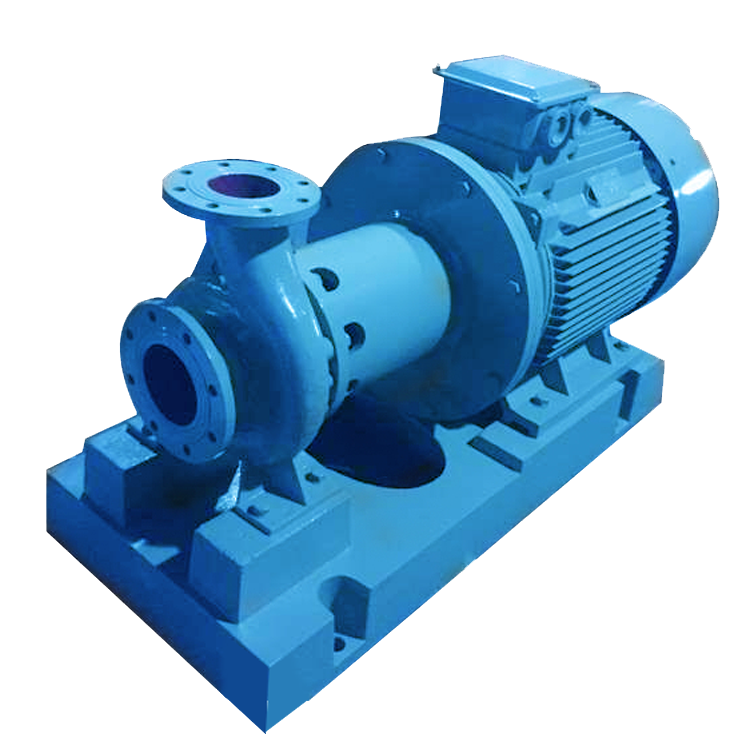
12. What process conditions should be met before the maintenance of chemical pumps? Answer: 1) Parking; 2) Cooling down; 3) Pressure relief; 4) Cut off the power supply; 5) Permutation;
13. What are the general principles for mechanical disassembly? Answer: In general, the parts should be disassembled first from the outside to the inside, from top to bottom, and in sequence. For overall parts, it is best to disassemble them as a whole.
14. What is the power loss inside a centrifugal pump?
Answer: There are three types of losses: hydraulic loss, volumetric loss, and mechanical loss.
1) Hydraulic loss: When the fluid flows in the pump body, if the flow channel is smooth, the resistance will be smaller, while if the flow channel is rough, the resistance will be greater. When the water enters the rotating impeller or flows out of the impeller, collisions and vortices will also occur, causing losses. The above two types of losses are called hydraulic losses.
2) Volume loss: The impeller is rotating, while the pump body is stationary. A small portion of the fluid flows back to the inlet of the impeller in the gap between the impeller and the pump body;
In addition, a portion of the fluid flows back from the balance hole to the impeller inlet, or leaks from the shaft seal.
If it is a multi-stage pump, there will also be some leakage from the balance plate, and these losses are called volume losses;
3) Mechanical loss: When the shaft rotates, it will rub against bearings, packing, etc. The impeller will rotate inside the pump body, and the front and rear cover plates of the impeller will rub against the fluid, consuming a portion of power. These losses caused by mechanical friction are collectively referred to as mechanical losses.
15. What is the basis for finding balance of rotors in production practice?
Answer: Depending on the number of revolutions and structure, static balance method or dynamic balance method can be used.
The balance of a rotating body can be solved using the static balance method. Static balance can only balance the imbalance of the center of gravity of a rotating body (i.e., eliminate torque), but cannot eliminate the imbalance couple.
Therefore, static equilibrium is generally only used for disc-shaped rotating bodies with relatively small diameters. For rotating bodies with larger diameters, dynamic balancing problems are often common and prominent, so balancing treatment is necessary.
Therefore, static equilibrium is generally only applicable to disc-shaped rotating bodies with relatively small diameters. For rotating bodies with larger diameters, dynamic balancing problems are often prominent and common, so balancing treatment is necessary.
16. What is balance? How many types of balance are there? Answer: The work of eliminating the imbalance of rotating parts or components is called balancing; 2) Balance can be divided into two types: static balance and dynamic balance.
17. What is static equilibrium? Answer: The method of finding balance is called static balance, which involves measuring the front position of the rotating part's imbalance on some specialized fixtures without the need for rotation, and also determining the position and magnitude of the balance force to be applied.
18. What is dynamic balance? Answer: When rotating parts, balancing not only the centrifugal force generated by the eccentricity, but also the balance of the force couple moment composed of the centrifugal force is called balance.
Dynamic balancing is generally used for machines with high speed, large diameter, and particularly strict working accuracy requirements, and precise dynamic balancing must be performed.
19. How to determine the weight orientation of the balanced part when performing static balancing of rotating parts?
Answer: First, let the balanced part freely roll on the balancing fixture several times. If the last rotation is clockwise, the center of gravity of the part must be on the right side of the vertical centerline (due to friction resistance). At this point, make a mark with a white chalk at the lowest point of the part, and then let the part roll freely. If the last roll is completed in a counterclockwise direction, the center of gravity of the balanced part must be on the left side of the vertical centerline. Similarly, make a mark with a white chalk, and the center of gravity recorded twice is the biased direction.
20. When performing static balancing of rotating parts, then determine the size of the balancing weight?
Answer: First, turn the biased position of the part to the horizontal position, and add an appropriate weight at the maximum circle of the symmetrical position on the opposite side.
When choosing to add appropriate weight, one should consider the location of this point and whether it is possible to balance and reduce weight in the future. After adding appropriate weight, keep it in a horizontal position or slightly swing it, and then reverse the part 180 degrees to maintain its horizontal position. Repeat this process several times until the appropriate weight is determined to remain unchanged. Then, remove the appropriate weight and weigh it, which determines the gravity of the balance weight.
21. What are the types of mechanical rotor imbalance? Answer: Static imbalance, dynamic imbalance, and mixed imbalance.
22. How to measure the bending of the pump shaft? Answer: After the shaft is bent, it will cause imbalance of the rotor and wear of the dynamic and static parts. Place small bearings on V-shaped iron and large bearings on roller brackets. The V-shaped iron or bracket should be placed firmly, and then support the dial gauge with the stem pointing towards the shaft center. Slowly rotate the pump shaft. If there is bending, the dial gauge has a maximum and minimum reading per revolution. The difference between the two readings indicates the maximum radial runout of the bending, also known as wobbling.
The bending degree of the shaft is half of the shaking degree, and the radial runout of the shaft generally does not exceed 0.05mm in the middle and 0.02mm at both ends.
23. What are the three main types of mechanical vibration causes?
Answer:
1) Structural aspect: caused by manufacturing design defects;
2) In terms of installation: mainly caused by improper assembly and maintenance assembly;
3) In terms of operation, due to improper operation, mechanical damage or excessive wear.
24. Why is it said that rotor misalignment is an important reason for abnormal vibration of the rotor and early damage to the bearings?
Answer: Due to installation errors, rotor manufacturing, deformation after bearing, environmental temperature changes, and other factors, rotor misalignment may occur. Poor rotor alignment in the shaft system can change the actual working position of the rotor journal and bearings due to changes in coupling force. This not only changes the working state of the bearings, but also reduces the natural frequency of the rotor shaft system. Therefore, rotor misalignment is an important reason for abnormal rotor vibration and early bearing damage.
25. What are the standards for measuring and rechecking the roundness and taper of the shaft neck?
Answer: The ovality and taper of the measured and rechecked sliding bearing shaft diameter should meet the technical requirements, and generally should not exceed one thousandth of the diameter. The ovality and taper of the shaft diameter of the rolling bearing shall not exceed 0.05mm.
26. What precautions should be taken when assembling chemical pumps?
Answer:
1) Whether the pump shaft is bent, deformed, etc;
2) Whether the rotor balance condition meets the standards;
3) The gap between the impeller and pump casing;
4) Whether the compression amount of the mechanical seal buffer compensation mechanism meets the requirements;
5) The concentricity of the pump rotor and volute;
6) Is the centerline of the pump impeller flow passage aligned with the centerline of the volute flow passage;
7) Adjustment of clearance between bearings and end caps;
8) Adjustment of the gap between the sealing parts;
9) Whether the assembly of the transmission system motor and the variable (increase/decrease) speed reducer meets the standards;
10) Align the coaxiality of the coupling;
11) Whether the gap between the retaining rings meets the standard;
12) Is the tightening force of each connecting bolt appropriate.
27. What is the purpose of pump maintenance? What are the requirements?
Answer: Objective: To eliminate problems that exist after long-term operation by inspecting and repairing mechanical pumps.
The requirements are as follows:
1) Eliminate and adjust large gaps caused by wear and corrosion inside the pump;
2) Eliminate dirt, dirt, and rust inside the pump;
3) Repair or replace parts that do not meet the requirements or have defects;
4) The rotor balance test is qualified;
5) Check the coaxiality between the pump and the drive machine and ensure it meets the standards;
6) The test run is qualified, the information is complete, and it meets the requirements of process production.
28. What is the reason for the excessive power consumption of the pump?
Answer:
1) The total head does not match the pump head;
2) The density and viscosity of the medium do not match the original design;
3) Inconsistent or bent pump shaft and prime mover axis;
4) There is friction between the rotating part and the fixed part;
5) Wear on the impeller retaining ring;
6) Improper installation of seals or mechanical seals;
29. What are the reasons for rotor imbalance?
Answer:
1) Manufacturing errors, uneven material density, different axial degrees, non rounded corners, and uneven heat treatment;
2) Incorrect assembly: The centerline and axis of the assembled components are different from the axis;
3) The rotor undergoes uneven deformation and wear, and the shaft deforms under operation and temperature.
30. What is a dynamically unbalanced rotor? Answer: There exists a rotor with equal size, opposite direction, and unbalanced particles combined into two force couples that are not on a straight line.